Edição 119 2008
|
 |
|
Usinas não precisam mais abrir todos os equipamentos na entressafra – basta consultar sistemas de monitoração para saber quais máquinas precisam de reparos |
Divulgação/SKF
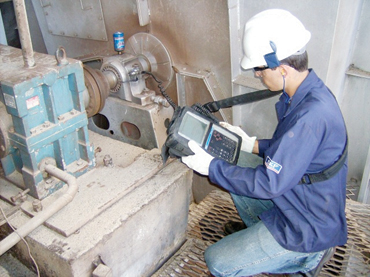 |
|
Análise de vibração: técnica preditiva indica possibilidade de falhas antecipadamente |
|
Até o final de março e início de abril, as usinas sucroalcooleiras do Centro-Sul, que processaram 480 milhões de toneladas de cana no ciclo 08/09, estarão fechadas para organização da próxima temporada. Mas a atual entressafra tem um contexto diferente. Chegou precedida por dois movimentos que abalaram o setor recentemente: dois anos de preços ruins para açúcar e etanol, e o agravamento da crise financeira mundial, que restringiu a oferta de crédito no Brasil.
Poucas vezes na história da cana-de-açúcar no Brasil, a redução de custos foi uma meta tão perseguida quanto agora – foco direcionado para manutenção na atual entressafra. Cálculos de consultores e usinas apontam que a atividade representa 40% do custo industrial de uma planta sucroalcooleira.
Mas especialistas garantem que a manutenção representa um dos principais custos operacionais controláveis nas indústrias. “É possível reduzir o gasto”, garante o consultor Anderson Trigo, diretor executivo da Spectra Monitoramento de Equipamentos. “Mas é preciso agir corretamente para não provocar o efeito inverso: aumentar os custos no futuro”, pondera.
Segundo especialistas, em épocas de crises, é comum empresas recorrerem a demissões, reduções nos investimentos em treinamento e até diminuição de reparos em equipamentos – a última alternativa deve a ser a opção de muitas usinas nesta entressafra.
De acordo com o Centro das Indústrias do Setor Sucroalcooleiro e Energético (Ceise Br), haverá redução acentuada nos serviços de manutenção. “Acredito que muitas usinas deixarão de fazer reparos e vão priorizar apenas os consertos essenciais”, diz o presidente da entidade, Mario Garrefa.
De acordo com diretor da Welding Soldagem e Inspeções, Márcio Perticarrari, a estratégia é arriscada. Para ele, esses expedientes até levam a uma redução imediata de custos, mas a médio e longo prazo os gastos podem aumentar significativamente. “Implicará em aumento de custo futuro com reparos e haverá maior risco de paradas não programadas”, diz.
Para os especialistas, a manutenção exige atualmente um novo sistema de gestão, com foco na antecipação aos problemas - e conseqüente redução de custos aliada à garantia de disponibilidade. “O custo aumenta muito com a realização de restaurações. Quanto mais consertos, mais custo. Assim, evitar reparos é diminuir custos”, descreve o engenheiro mecânico Adyles Arato Junior, autor do livro ‘Manutenção Preditiva usando Análise de Vibrações’.
Mas ainda não é assim que a maioria das usinas sucroalcooleiras gerencia suas atividades de manutenção no Brasil. A característica sazonal da operação do setor sucroalcooleiro determinou o plano estratégico que prevalece no segmento: a manutenção de entressafra.
Os especialistas classificam a atividade como ‘cadeia da revisão desnecessária’. O procedimento não considera a cultura de busca da causa raiz de falhas e se baseia na intervenção em todos os equipamentos e substituição de todas as peças de desgaste.
A troca é motivada por precaução. “Muitos componentes que poderiam ter mais tempo de vida útil acabam sendo substituídos. Como a usina não conhece a situação do produto, faz preventiva para garantir que o equipamento vai operar durante determinado período de tempo sem quebrar na safra”, explica Trigo.
Quando predomina essa filosofia de trabalho, os resultados são negativos sobre a gestão e o controle de custos, porque se torna difícil controlar os gastos. Segundo Arato, o valor do reparo pode atingir de 20% a 40% do preço do equipamento, de acordo com a complexidade e porte da máquina. Se o prazo do conserto interferir na produção, ainda é necessário avaliar as perdas provocadas pela parada imprevista.
Dados da última pesquisa da Associação Brasileira de Manutenção (Abraman) revelam que muitas empresas ainda gastam mais com manutenção do que o necessário. O levantamento representa uma detalhada análise da situação da função em todo o Brasil – o documento considera vários tipos de indústrias. Embora o setor sucroalcooleiro não informe seus dados, especialistas acreditam que os resultados também refletem o panorama deste segmento.
A pesquisa revela que apenas 20,33% das empresas brasileiras possuem Plano de Controle de Custos e somente 9,75% monitoram freqüência de falhas. “Esses números demonstram que a grande parcela da indústria continua correndo atrás dos problemas para conseguir produzir”, afirma o consultor Márcio Cotrim, diretor da MC Consultores.
Além de custo alto, a revisão desnecessária poderá induzir quebras inesperadas durante a safra – é a chamada “curva da banheira”. Segundo Trigo, após a intervenção, a probabilidade de ocorrer uma falha aumenta, porque uma série de variáveis pode ser alterada.
Em geral, depois da partida de uma máquina, a chance de falha cai gradativamente até alcançar possibilidades mínimas - é quando o equipamento encontrou seu equilíbrio dinâmico. “Mas a partir do momento em que a empresa abriu e mexeu no equipamento, há risco de ter inserido um problema. Por isso, a manutenção preventiva custa caro e nem sempre garante bom funcionamento durante a safra”, defende o diretor da Spectra. |
Divulgação/Cerradinho
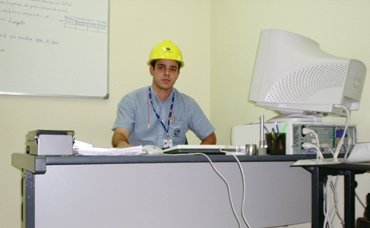 |
|
Rodrigo Pazotto, da Cerradinho: economia de até 85% de manutenção em alguns equipamentos |
|
Manutenção Centrada na Confiabilidade
A única maneira de evitar o problema é realizar uma análise e pré-definir quais equipamentos precisarão ser reparados. Mas, para identificar essa necessidade, é preciso manter um sistema de monitoramento dos equipamentos durante a sua utilização no período de produção que defina claramente seu estado.
O uso de novas técnicas, como o monitoramento constante, é um dos pré-requisitos de uma nova filosofia que começa a crescer no setor sucroalcooleiro nacional com a chegada de grupos estrangeiros e com profissionalização das companhias nacionais: a Manutenção Centrada na Confiabilidade (MCC).
O objetivo da Manutenção Centrada na Confiabilidade é assegurar que qualquer ativo físico (equipamento) opere da maneira desejada pelo usuário no seu contexto operacional presente. “A meta do projeto é não deixar a máquina quebrar e aumentar a probabilidade de o equipamento funcionar bem”, resume Trigo. “Além disso, prevê conhecer os motivos de uma quebra e orientar a empresa a agir para não deixar a falha acontecer novamente”, completa.
A filosofia demanda, portanto, a aplicação de um conjunto de técnicas que impeçam a mortalidade infantil do equipamento. Nesse contexto, a manutenção preditiva ou monitoramento da condição dos equipamentos através de parâmetros se torna uma das práticas mais adequadas para indicar o nível de confiabilidade das máquinas.
Segundo Trigo, a técnica preditiva fornece a matéria-prima da metodologia de Manutenção Centrada na Confiabilidade: a informação. “A tomada de decisão, de intervir ou não, não é mais fundamentada em intervalos de tempo. Passa a ser baseada na informação. Esses dados indicarão a possibilidade de quebra e falha e permitirão programar uma parada”, explica.
A informação principal apurada é a evolução do desgaste com base em um gráfico de tendência (valor do parâmetro monitorado) ao longo do tempo. O dado complementar é a indicação de um defeito ainda em fase inicial, por meio de uma análise mais apurada.
Para atender as necessidades da MCC, a tecnologia de monitoração da manutenção preditiva deve permitir a coleta de dados com o equipamento em funcionamento ou mínima interferência possível no processo, sem necessidade de desmontagens.
O atendimento a esses requisitos demanda o uso de algumas técnicas. As mais aplicadas atualmente no setor sucroalcooleiro são: análise de vibração, termografia, análise de óleo e temperatura e ensaios não destrutivos.
Segundo especialistas e usinas já adeptas à tecnologia, as principais vantagens da medição e interpretação de informações que permitem antecipação a quebras são redução de custos com reparos desnecessários e consertos futuros – há ainda queda de gastos com estoques de peças de reposição. “As reduções de paradas não programadas de equipamentos são da ordem de 25%. Também há diminuição de Tempo Médio Para Reparo (TMPR) e aumento de Tempo Médio Entre Falhas (TMEF)”, aponta o consultor Cotrim.
Benefícios como esses estão sendo experimentados pela Unidade Potirendaba do Grupo Cerradinho. Inaugurada em 2006, a usina já nasceu com a filosofia de Manutenção Centrada na Confiabilidade. A planta tem disponibilidade anual de 97%, já considerando paradas para chuvas – a média no setor é de 92%. |
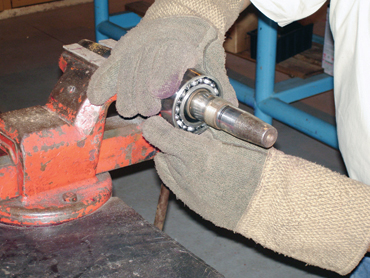 |
Troca de rolamento por precaução durante a entressafra: componente poderia ter tempo de vida útil maior |
|
Análise de investimento
Embora proporcione vantagens em aumento de disponibilidade e redução de custos, a técnica é cara, porque demanda uso de tecnologia moderna e exige mão-obra qualificada. Por isso, a seleção dos equipamentos que serão monitorados exige análise criteriosa.
Trigo recomenda a avaliação de dois critérios fundamentais: importância da máquina no processo e custo do reparo do equipamento. Para analisar o retorno do investimento, a usina precisa comparar o valor da preditiva somada ao gasto com as intervenções corretivas que continuam necessárias com o custo da ação preventiva em todos os itens na entressafra.
Segundo Trigo, em geral, o resultado dessa conta indicará uso da preditiva. “Temos tido resultado de redução de custo de 40% no valor da manutenção nas máquinas que são monitoradas”, assegura.
A conta, com base nos gastos da matriz do Grupo Cerradinho, incentivou a empresa a adotar a técnica na unidade Potirendaba. “Já tivemos redução de custos de até 85% com essas análises. A preditiva precisa de investimento, mas é barata perante a manutenção preventiva de entressafra”, diz o engenheiro encarregado pela manutenção industrial da planta, Rodrigo Pazotto.
Para exemplificar, Pazotto relata um caso ocorrido na última entressafra, quando enviou dois picadores e dois desfibradores para reforma em uma empresa especializada, que, baseada em análise visual, reprovou todos os rolamentos das máquinas – a troca exigiria investimento de R$ 120 mil. “Mas o nosso monitoramento indicava que os rolamentos estavam bons e ainda tinham vida útil. Rodaram normalmente na safra seguinte”.
Embora os resultados sejam animadores, os especialistas garantem que somente a manutenção preditiva não assegura o sucesso do projeto – a corretiva e a preventiva ainda são necessárias. “Nunca se deve aplicar uma técnica específica apenas e esperar algum retorno retumbante. Não existem milagres neste setor”, argumenta Arato.
Márcio Perticarrari, da Welding, completa que a compra técnica criteriosa de produtos e serviços também reduz significativamente a manutenção. “Não se deve fazer economia nesta hora”.
A expansão do setor sucroalcooleiro no Brasil e a necessidade competitividade ainda mais acentuada pelos movimentos de preços baixos e crise financeira mostram que o segmento tende a rever a cultura de prioridade ao melhor preço em detrimento ao melhor custo final.
Para Trigo, esse é um movimento irreversível. “Quem não aderir está fadado a perder competitividade no futuro”. Não é o caso do Grupo Cerradinho. O agravamento da crise financeira não mudou os planos da empresa para 2009. A companhia confirmou investimentos para inaugurar sua terceira unidade no próximo ano, a Usina Porto das Águas, localizada em Chapadão do Céu/GO. “Para passar por crises, só com custo baixo. Não mudamos o cronograma da nova unidade porque a gente se preparou para reduzir custos”, conclui Pazotto. |
|
Elemento humano é fundamental para sucesso do projeto |
Mesmo com uso de técnicas avançadas de monitoramento, a estratégia da Manutenção Centrada em Confiabilidade pode falhar no objetivo de reduzir custos. Segundo especialistas, as mudanças tecnológicas devem ser acompanhadas de alterações na estrutura organizacional e cultural da empresa.
Para o engenheiro mecânico Adyles Arato Júnior, a alteração cultural prevê a adoção da postura de que a manutenção é um insumo da produção. Assim, essas duas áreas e a engenharia da empresa devem ter pontos de interseção - e não se comportarem como departamentos totalmente independentes um dos outros.
A estratégia também demanda mudança de comportamento e atitude de todos os manutentores, iniciativa comandada por gerente e supervisores. Segundo o consultor Anderson Trigo, a grande mudança de paradigma é transformar o plantel de profissionais técnicos alocados nas oficinas elétricas e mecânicas para conserto de equipamentos em equipes de inspeção. “De consertadores de defeitos passam a ser vigilantes para evitar que eles aconteçam”, resume.
Esse novo elemento introduzido na organização da empresa é o ‘homem preditivo”. A atividade principal deste profissional é coletar e manipular dados no campo até transformá-los em informação estratégica. “Para ser bem objetivo, é aquele que consegue manter o processo produtivo, equipamentos, instalações e ambiente, dentro das condições exigidas”, explica o consultor Márcio Cotrim.
De acordo com Cotrim, essa é outra grande revolução cultural proposta pelo modelo de MCC. Há alguns anos, um manutentor bem sucedido era aquele profissional capaz de executar um bom reparo no equipamento. Atualmente, o homem de manutenção deve ser treinado, orientado e incentivado para não precisar fazer nenhum conserto - ou seja, para conseguir evitar as quebras não planejadas, através de inspeções rotineiras, acompanhamento de desempenho e mudança de atitude.
Esse contexto transforma o elemento humano em peça chave para o sucesso do projeto, que depende muito do volume e qualidade de dados e informações obtidos sobre os equipamentos monitorados. “Costumo dizer que somos um time de futebol. A empresa que monitora é o meio de campo. A idéia não é ela fazer gol. Isso cabe ao centroavante, que é o mecânico”, compara Trigo.
Segundo o consultor, quando a empresa vai fazer a análise de vibração, permanece no máximo cinco minutos em contato com a máquina. Já o operador fica ao lado do equipamento o dia todo. “O mecânico abre a máquina, ele sabe como ela está por dentro, de que lado havia desgaste, por exemplo. São informações que só ele tem. É importantíssimo conversar com esse profissional para fechar um diagnóstico”.
Os especialistas reconhecem, porém, que a mudança cultural inicialmente é difícil e exige um longo processo de convencimento. De acordo com Trigo, os mecânicos, em geral, entendem que alguém está invadindo uma área deles. Cotrim também atribui a restrição inicial à necessidade de aprendizado. “É mais fácil usar as mãos do que a cabeça. Mas para se ter confiabilidade precisa ser usada mais a cabeça, para pensar, analisar e intervir com certeza”, diz. A estratégia de persuasão deve considerar, portanto, paciência e persistência. |
Divulgação/Cerradinho
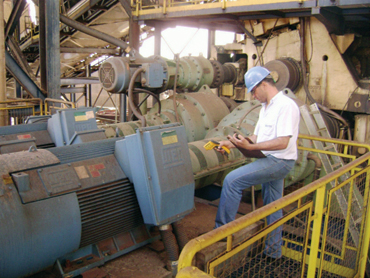 |
|
O “Homem Preditivo”: principal responsável pela manutenção do processo produtivo dentro das condições exigidas |
|
LEIA A MATÉRIA NA ÍNTEGRA NA EDIÇÃO
IMPRESSA |
Desejando saber mais sobre a matéria: redacao@editoravalete.com.br |
|
|
Atualidades
Estado quer reduzir água na aplicação de defensivos
Setor pode exportar mais de 7,5 mil MW em 2009
Brasil terá 571,4 mi toneladas de cana em 08/09 |
Excelencia sustentável
Atender normas e práticas sustentáveis custa caro
|
|
|
|