Edição 118 2008
|
 |
|
Necessidade de respostas rápidas e precisas para atendimento de demandas com máxima produtividade e qualidade, redução de custos e margens, evidencia soluções geradas pela integração total da automação
|
|
|
Sistema de moagem da Usina Santo Inácio: controle eficaz da produção revertido em ganhos na qualidade e redução de custos |
|
Quando decidiu inaugurar a Santo Inácio, em junho de 2007, o Grupo Alto Alegre percebeu que a usina precisava nascer contextualizada com o novo ambiente global do mercado sucroalcooleiro. A companhia entendeu que a implantação de tecnologias para melhoria da gestão de informações poderia estruturar sua planta para uma realidade mais produtiva.
O conceito descartava, já no projeto, a administração de processos manuais que geram erros, atrasam o retorno de informações importantes para avaliações, planejamentos e controle de custos, por exemplo. Para deixar a Santo Inácio pronta a atender às necessidades do mercado local e internacional, o Grupo Alto Alegre decidiu adotar novas soluções em mobilidade - e pioneiramente no Brasil iniciou o processo de integração total da automação instalada na planta.
O conceito da automação integrada compreende a configuração comum e uniforme de todos os componentes do sistema de automação, com gerenciamento comum dos dados em uma única base e comunicação interligada, baseada em redes (Profibus e Ethernet, por exemplo), com acesso a todas as informações on line e em tempo real.
Com a integração da automação, a usina deixa de ter áreas dispersas com soluções distintas. Os vários departamentos da planta – moagem, destilaria, elétrica, por exemplo – trocam informações o tempo todo, monitorados por um único centro de controle, o COI. O parque industrial também passa a enviar dados para a administração por interligação com os setores de tecnologia de informação e investimentos.
A arquitetura é diferente da configuração tradicional implantada na maioria das usinas brasileiras. Neste modelo, atuadores e sensores distribuídos por todas as áreas da planta monitoram equipamentos e devolvem essa informação para o controle. “Para isso, a usina pode ter várias ilhas diferentes de controle na planta. Cada uma operando por sua conta e independentes entre si”, descreve o gerente geral de automação industrial da Siemens, Pablo Roberto Fava.
Outra diferença é o uso de soluções distintas aplicadas em cada área da planta industrial – há vários produtos e dificuldade de integração e comunicação.
Um dado da geração de vapor necessário, por exemplo, para fabricação de açúcar não é disponibilizado facilmente. “O operador precisa perguntar a informação por rádio. Essa demora dificulta a tomada de decisões, como uma ação corretiva por parte da equipe de manutenção”, aponta o diretor técnico da Atma Automação, Paulo Lattaro.
A automação tradicional também se restringe ao chão-de-fábrica. O objetivo do controle é fazer com que o equipamento trabalhe da maneira desejada pela usina - oferece informação para o gestor do processo e não proporciona dados que possam interessar ao nível gerencial e administrativo.
Os especialistas apontam que esse conceito não atende mais as necessidades do setor sucroalcooleiro. Segundo eles, a automação não pode ser feita mais isoladamente nem com o objetivo único de comandar o processo.
“Hoje não existe mais uma célula produtiva. Existe uma unidade geradora de álcool, açúcar e energia. Isso necessita velocidades de atuação e de decisões que um ser humano com pranchetas na mão não consegue ter”, diz Lattaro.
A competição global tem exigido das empresas respostas cada vez mais rápidas e precisas, comprometimento com prazos com máxima produtividade e qualidade, redução de custos e margens.
Segundo o coordenador de automação do Grupo Alto Alegre, Aldemir Ernesto, o mercado muda diariamente e expõe as usinas a influências internas e externas, cenário que tem obrigado as empresas a se preocuparem com todos os aspectos do seu processo produtivo. “Essas atribuições eram satisfatórias com a utilização de apenas um software ERP. Hoje, porém tem-se a necessidade de outras fontes de informações”, explica. |
Divulgação/Siemens
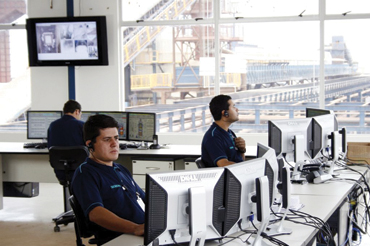 |
|
Centro de controle: os vários departamentos da planta trocam informações o tempo todo |
|
Vantagens da integração
Para aumentar a fonte de informações, a Santo Inácio - que processa 2,5 milhões de toneladas de cana e produz 125 milhões de litros de álcool por safra – utiliza uma arquitetura Cliente Servidor com redes Profibus e ASI no campo. Há ainda um centro de operações com todas as áreas do processo industrial agrupados em uma única sala.
Além das áreas relativas ao processo industrial, a usina também integrou os sistemas de Controle de Qualidade (LIMS) e pesagem de cana. Na atual safra está sendo realizado o processo de integração dos sistemas de manutenção industrial.
O processo de integração terá novas etapas nos próximos anos. O sistema ERP ainda não foi unificado. “Estamos analisando que nível de integração será necessário. Os sistemas de controle agrícola e manutenção industrial estão em processo de integração. A previsão é estarmos finalizando estes trabalhos na próxima safra”, comenta Ernesto.
A decisão pela integração foi baseada na observação do sistema de controle de outras duas unidades do Grupo, que tinham modelo de automação concentrado em ilhas, sem interligação. Também não havia banco de dados e, para ter acesso às informações, o gestor precisava ir até o local e verificar os gráficos existentes ou por meio de levantamentos - de acordo com cada situação, o tomador de decisão esperava alguns dias para conseguir as informações necessárias.
Atualmente todas as unidades foram padronizadas com a arquitetura Cliente Servidor. Segundo Ernesto, a configuração antiga se tornou insuficiente. “Devido à concorrência no setor, o mercado exige cada vez mais diminuir custos e aumentar a eficiência industrial. Tudo isso com qualidade superior. Mas, com a deficiência de aquisição das informações do processo, a arquitetura anterior não nos atenderia nos dias atuais”.
Com a automação integrada, o Grupo Alto Alegre vislumbra garantir ganhos com agilidade na tomada de decisões, redução nos custos de manutenção ao longo da vida útil da planta e qualidade no processo todo – para atender a demanda dentro dos prazos e características desejadas.
O conceito preenche o espaço vazio que existia entre os sistemas de gestão corporativa e o chão-de-fábrica. A automação tradicional fornece dados apenas para o processo. Com a integração e evolução tecnológica, os equipamentos transmitem informações extras: tempo de uso da máquina, vida útil, número de série, versão.
“São dados que não interessam para o processo.A usina não vai fazer mais ou menos álcool por isso. Mas são informações relevantes para a administração”, observa o engenheiro Marcus Vinícius Ribeiro, gerente de engenharia de aplicação do setor de Açúcar e Álcool da Smar.
A integração com uso de programas PIMS e MES proporciona a troca direta de informações entre a manufatura e os sistemas de CRM SCM e ERP. Além do chão-de-fábrica, interligam dados de produção e de faturamento. De acordo com Ernesto, o resultado é a potencialização do sistema de negócios com informações precisas, confiáveis e on-line.
“O sistema integrado permite dinâmica empresarial e oferece segurança nas tomadas de decisões, que passam a ser fundamentadas em informações precisas e coordenadas. Indubitavelmente esta é a melhor ferramenta de gestão para uma empresa que deseja atender o novo cenário do mercado global”, frisa o coordenador do Grupo Alto Alegre.
|
|
Tomada de decisão e manutenção
Devido às restrições tecnológicas e a falta de uma base de dados, as informações do Grupo Alto Alegre eram procuradas somente quando as usinas apresentavam alguma anomalia ou ocorrência. Atualmente, com as facilidades do sistema integrado, o gestor está constantemente monitorando o processo por meio de telas sinóticas e gráficos - tudo em tempo real.
Para Ernesto, o principal benefício é a democratização das informações do chão-de- fábrica e a sua integração aos sistemas de gestão da empresa. “A tecnologia proporciona aos gestores uma imagem real de como está o processo produtivo e quais medidas podem ser tomadas para correção ou melhoria. Isso, com certeza, vai refletir em redução de custos e ganho de qualidade”, acredita.
Com este sistema, o gestor pode decidir, por exemplo, se é mais vantajoso fabricar açúcar em épocas de preços baixos para álcool observando a tendência de produção da usina e as demandas já contratadas. No processo tradicional, para tomar essa decisão, o administrador precisava marcar reunião com subordinados.
No conceito tradicional, quando um integrador de processos toma a decisão, de aumentar ou diminuir a moagem, por exemplo, os resultados são sentidos no departamento financeiro depois de alguns meses, quando se constata que a produção não atingiu a meta planejada.
“Isso acontece porque o tráfego de informações é lento, leva tempo para chegar aos níveis administrativos. E voltar atrás no tempo não tem jeito. Com a automação integrada, a informação chega a todos os departamentos em segundos”, afirma Ribeiro, da Smar.
Além da melhor qualidade de informação transmitida ao administrador, a integração da automação proporciona, ao gestor de processo, redução do tempo de manutenção, dizem os especialistas. Segundo Fava, da Siemens, a solução com gerenciamento de ativos permite a antecipação a possíveis quebras, o que também reduz a possibilidade de paradas indesejadas e aumenta a disponibilidade da planta.
“A entressafra antigamente durava de novembro a abril. Havia tempo para desmontar tudo, Hoje, é entre final de dezembro a início de março. Existia uma situação em que a sazonalidade do mercado permita uma ação de manutenção. Com a solução integrada, a usina consegue saber efetivamente o que precisa de correção e agir apenas nesses equipamentos”, detalha.
Um exemplo é a existência hipotética de instrumento de pressão que media a variável da caldeira a 42 kg. Por algum motivo, o índice começa a cair, mas o equipamento não acusa o problema. Atualmente, o instrumento possui capacidade de processamento que permite auto-diagnóstico. Com a integração, a informação sobre a falha chega a todos os setores da usina em tempo real.
“A equipe de manutenção consegue sair para o campo para dar a correção já sabendo onde é a falha. Antes tinha que parar o equipamento para descobrir o problema. A tomada de decisão era muito mais difícil. Dar manutenção é gastar dinheiro. Quanto menos der, menos recurso a usina gasta. A usina integrada pára hoje muito mais por chuva do que por problema mecânico”, aponta Lattaro. |
|
|
Competitividade global: contexto necessita velocidades de decisões que um ser humano com pranchetas na mão não consegue ter |
|
Benefícios da integração
- Redução do tempo de engenharia
- Aumento de produtividade
- Reconhecimento e eliminação rápida de erros e falhas
- Redução de tempo de paradas
- Aumento da disponibilidade da planta
- Redução dos custos de ciclo de vida e Respostas rápidas a mudanças da situação do mercado
- Acompanhamento para manutenção e diagnose remota do sistema durante a safra
- Redução drástica na infra-estrutura de cabeamento
- Inclusão de novos equipamentos durante a safra sem a necessidade de parar a produção
Fonte: Siemens, Smar, Atma e Grupo Alto Alegre |
Tendência irreversível
Todas essas vantagens já começam a fazer parte da realidade das usinas do Grupo Alto Alegre. “Com a integração das áreas e seus sistemas de gestão com o chão-de-fábrica, estamos aprimorando o processo de gestão da empresa. As informações geradas através desta integração vão ser fundamentais para a melhoria contínua do processo”, afirma Ernesto.
Além do controle eficaz da produção, os dados serão fonte de informação imprescindível para o planejamento de novos investimentos do Grupo. Para Ernesto, esse diferencial vai resultar em ganhos na qualidade e redução de custos, que são os requisitos do mercado global.
Como ressalta o gerente da Alto Alegre, a integração está se tornando uma necessidade para as usinas brasileiras. Outros investidores estão atentos à tecnologia. “Hoje, não vendemos plantas novas sem relés inteligentes e protocolos de comunicação. A evolução tecnológica acelerou muito expressivamente nas usinas, principalmente nos projetos novos”, conta Fava.
Mas o conceito ainda é recente no Brasil – a primeira aplicação foi realizada em 2004. No universo atual de cerca de 400 usinas em operação, o modelo está restrito a pouca unidades. A disseminação total ainda deve demorar alguns anos.
A tendência, porém, é considerada inevitável. “O mercado está mais acirrado, a usina tem que produzir produto de melhor qualidade, com menor custo possível. As usinas que não forem para esse caminho correm o risco de serem improdutivas”, conclui Ribeiro.
|
Divulgação/Welding
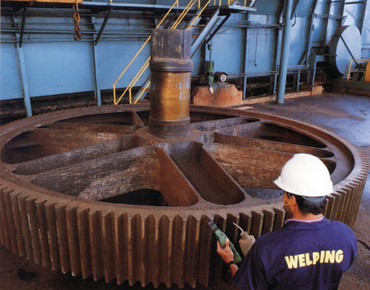 |
|
Tempo para manutenção corretiva diminuiu: com solução, reparos são feitos apenas em caso de necessidade |
|
Integração de automação a TI também agiliza decisão
Uma das próximas etapas do projeto de interligação da Usina Santo Inácio é integrar a automação à tecnologia de informação, ou seja, unificar a área de produção aos departamentos agrícola e laboratorial, sempre com foco no fornecimento de informações aos gestores dos setores correlacionados.
A integração será realizada pelo software Simatic IT, da Siemens. Por meio dessa ferramenta, todas as informações ficam centralizadas e disponibilizadas em forma de indicadores (kpi) para agilizar a tomada de decisão do nível gerencial da planta. “A disponibilidade em tempo-real deste tipo de informação aumenta a produtividade industrial, melhora a eficiência, disponibilidade e qualidade na planta; e potencializa o lucro obtido por tonelada de cana processada”, garante o engenheiro de suporte em automação da Siemens, Fábio Elias.
A solução oferece em tempo real dados detalhados sobre a qualidade da cana que está chegando à indústria para ser processada. Análises de amostras no laboratório podem indicar o tempo entre a queima e o transporte para a usina e se as características daquela matéria-prima podem render mais para álcool ou açúcar.
Essas informações podem ser analisadas on line no sistema de gerenciamento de laboratório. No processo tradicional, os dados permanecem centralizados no laboratório e demora até serem conhecidos por gerentes e supervisores de produção – essa lentidão atrasa a tomada de decisão.
Com a informação sobre a qualidade da cana e baseado em indicadores de processo, estoque nos tanques, material disponível e análises de mercado, o gestor pode decidir como aproveitar melhor a matéria-prima: se o cenário é melhor para produzir açúcar ou álcool. “É uma informação que ele pode ter rapidamente para analisar com qual produto teria mais retorno”, diz Elias.
No processo tradicional, a decisão é reativa e pode demorar para ser tomada. “Estamos antecipando as informações para que as pessoas possam tomar a decisão que melhor aproveite a qualidade da matéria-prima e aumentar a eficiência do processo. Para isso, tem que ter integração entre automação e Tecnologia de Informação”, conclui o engenheiro da Siemens.
|
|
|
Chegada da cana na indústria: com informações sobre qualidade, gestor pode decidir se fabrica açúcar ou álcool
|
|
LEIA A MATÉRIA NA ÍNTEGRA NA EDIÇÃO
IMPRESSA |
Desejando saber mais sobre a matéria: redacao@editoravalete.com.br |
|
|
Atualidades
CTC lança variedades super precoces |
Empresas
Comanche Canitar surge com alto nível de automação
|
Retrospectiva
Realizadas antes da crise, Fenasucro & Agrocana apresentam resultados positivos
|
|
|
|