Edição 111 2007
|
 |
Conceito mais difundido
|
Divulgação/Uni-systems
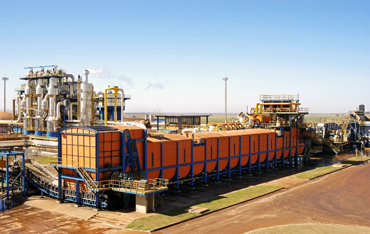
|
|
Difusor instalado em usina brasileira: produto ganha uma situação de comércio favorável |
|
Limitado a oito unidades em funcionamento até 2004, difusor já soma 22 equipamentos vendidos – aumento é principalmente pela instalação de usinas em novas fronteiras da cana |
A Dedini anunciou recentemente um acordo de transferência de tecnologia com a companhia Bosch Projects, da África do Sul. O contrato prevê que a empresa nacional projete, fabrique e monte um novo modelo de difusor no Brasil. O investimento, que poderia ser considerado um empreendimento comercial de risco até a pouco tempo atrás, representa uma aposta no aquecimento do mercado dos sistemas de extração de caldo por difusão. A atual base nacional de sistemas de extração do caldo está quase unanimemente baseada em moendas. Instalado no Brasil pela primeira vez em 1985, na Usina Galo Bravo, o difusor tinha apenas oito unidades em funcionamento até 2004, em um universo de 347 usinas em operação. Aplicações mal sucedidas no passado e conceitos contrários à eficiência do difusor ofereceram o domínio do mercado às moendas. "Também não havia muito interesse no desenvolvimento do difusor. Existiam muitas empresas que vendiam moendas e ternos, além de firmas especializadas na manutenção dos equipamentos. Era um produto de segmento comercial muito forte", lembra o gerente de projetos da Uny-Systems, Márcio Fonseca. A recente expansão canavieira, porém, reuniu um conjunto de demandas favoráveis ao difusor que começam a expor as moendas à concorrência: instalação de usinas nas novas fronteiras da cana, implantação de projetos de plantas de açúcar e/ou álcool combinados com co-geração de energia e projetos de modernização de usinas existentes. Essas circunstâncias evidenciaram a necessidade por características mais comuns aos difusores. "O maior índice de extração, a possibilidade de economia de energia mecânica e os menores custos com manutenção passaram a influenciar a opção por difusores. Com isso, o produto ganha uma situação de comércio muito favorável", descreve Fonseca. Segundo dados da Dedini, até o final do primeiro semestre deste ano, das 393 usinas com sistema de extração definidos no Brasil (unidades em operação e plantas novas), 22 optaram por difusores – nem todos estão em funcionamento, pois alguns equipamentos ainda não foram entregues. O aumento é motivado sobretudo pelos projetos de usinas que partem do zero. Do final de 2004 até o dia 30 de junho de 2007, dos 46 projetos de usinas novas, 12 decidiram pelo uso do equipamento. De acordo com a Dedini, o volume representa 26,1% das decisões por sistemas de extração em novas unidades. "Isso mostra que começa a haver uma avaliação forte sob o uso do equipamento. Atualmente todas as novas usinas pelo menos cotam o difusor", avalia o vice-presidente de operações da empresa, José Luiz Olivério. Os dados da Uni-Systems corroboram a tese. Principal fornecedora de difusores no Brasil, a empresa vendeu nove unidades de 1985 a 2005 – mesma quantidade negociada apenas em 2006. "Devemos repetir esse balanço no final deste ano", calcula Fonseca. O interesse não é medido apenas pelas vendas concretizadas. A Uni-Systems realizou 30 palestras sobre o funcionamento do difusor em 2006 e deve terminar 2007 com número semelhante de apresentações. Para atender a demanda, a empresa promoveu uma remodelação na sua equipe de engenharia, que era composta por dois profissionais até 2005 – atualmente são 11.
Principais atrativos
Para Marcos Fonseca, embora seja uma característica conhecida desde o lançamento da tecnologia, a capacidade do difusor de extrair índices maiores de caldo tornou-se mais necessária no atual cenário de crescimento do setor sucroalcooleiro. Desde que seja operado de acordo com as suas especificações de projeto, o difusor pode atingir níveis de extração entre 97,5% a 98,5% - as moendas, que até a alguns anos atrás alcançavam no máximo 96%, atualmente conseguem dados de 96,5% a 97,5%. "O interesse pelo difusor é maior porque atualmente as usinas têm uma preocupação grande em evitar perdas, o que não acontecia antigamente", define o gerente de projetos da Uni-Systems. Conforme cálculos da empresa, o pol% no bagaço originário do difusor pode chegar a 0,7%, mantendo-se, na maioria dos casos, abaixo de 1,0%. Comparando-se com situações práticas de moagem existentes com pol% no bagaço de 1,6% a 2,3%, este resultado representa um aumento de aproximadamente US$ 700 mil a US$ 800 mil para cada 1 milhão de toneladas de cana processadas – a avaliação considera o parâmetro de recuperação de açúcares. Segundo Fonseca, a maior parcela das novas plantas apresenta projetos para processamento de 4 a 6 milhões de toneladas – no passado as unidade geralmente optavam por sistemas para moagem de 1 milhão. "Isso significa que uma planta nova de 4 milhões de toneladas recupera de US$ 3,2 milhões a US$ 4 milhões". Ele ressalta que valor que pode variar de acordo com a remuneração oferecida ao açúcar no mercado. A possibilidade de maiores índices de extração foi parâmetro decisivo para a escolha do difusor pela Usina São Francisco, que iniciou operações no ano passado em Quirinópolis, interior de Goiás, localizada a 300 quilômetros da capital, Goiânia. Segunda unidade do Grupo São João, a São Francisco planeja processar 1,6 milhão de toneladas de cana na safra atual, com projeto de expansão para 4,5 milhões de toneladas a partir da safra 2009/2010. Embora a unidade matriz, a USJ, localizada em Araras/SP, seja equipada com duas moendas (uma com 6 ternos 42" x 84" e a outra com 2 ternos 42" x 84" e mais 4 ternos intermediários 36" x 78"), estudos de viabilidade do Grupo indicaram a escolha pelo difusor. "Optamos por difusor devido a sua simplicidade operacional, maior extração de açúcar da cana e menor custo operacional, além de menor custo de manutenção", descreve o engenheiro José Ieda Neto, gerente industrial do Grupo São João. |
|
Menor custo de manutenção
Assim como a unidade São Francisco, os três novos projetos da Companhia Nacional de Açúcar Álcool (CNAA) - criada pelas empresas associadas Companhia Energética Santa Elisa e o Açúcar e Álcool Fundo de Investimentos e Participações (FIP) – também optaram pelo difusor. Instaladas em Minas Gerais e Goiás, as quatro usinas estão localizadas em locais considerados novas fronteiras agrícolas, distantes dos principais centros fornecedores de tecnologia e serviços de manutenção. "Para evitar paradas na fábrica e demora para reposição de peças ou consertos, as usinas preferem o difusor, que tem necessidade de manutenção menor", explica Olivério. Segundo os especialistas, o custo de manutenção do difusor é, em média, 35% a 40% inferior ao valor requerido por um tandem convencional com a mesma capacidade. "O menor custo de manutenção é fácil de entender: o processo de difusão emprega uma potência mecânica muito menor e, portanto, causa menor atrito, logo menor desgaste, que resulta em menor manutenção", resume o engenheiro Elmar Würch Filho, do departamento industrial da Monteverde Agro-Energética. O menor custo de manutenção também foi decisivo para a escolha da Usina Noroeste Paulista, de Sebastianópolis/SP, que está ampliando sua a linha de produção. Adquirida recentemente pelo grupo chinês Noble, a unidade, que moeu 1,1 milhão de toneladas na safra passada, vai aumentar o volume para 2 milhões de ton na temporada atual – o objetivo é chegar a 4 milhões de ton a partir do próximo ciclo. Na última entressafra, a usina modernizou a moenda, trocou quatro ternos e eletrificou totalmente o equipamento. Para atingir as 4 milhões de toneladas previstas, a Noroeste Paulista prevê a instalação da segunda linha de extração em agosto de 2008, quando começa a operar um difusor com capacidade inicial de processar 12 mil toneladas de cana/dia. "O custo de manutenção foi decisivo para a nossa escolha, estimamos que será de 40% a 50% menor em relação ao nosso outro sistema", revela o gerente industrial, César Miranda. Outro critério favorável ao difusor, segundo Miranda, foi o plano de aumento da atual produção de 88 milhões de litros por safra para 242 milhões de litros por temporada, quando a capacidade prevista de moagem for atingida. "O difusor produz caldo de melhor qualidade para álcool, com menos terra no bagaço devido a lixiviação", justifica. |
Divulgação/Uni-Systems
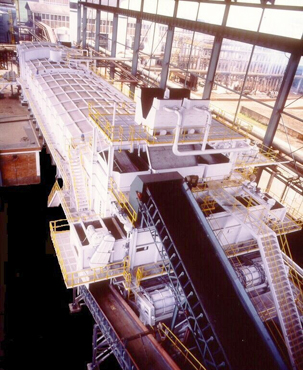
|
|
Custo de manutenção do difusor é, em média, 35% a 40% inferior ao valor requerido por um tandem convencional com a mesma capacidade |
|
Economia de energia mecânica
A Usina Noroeste também foi atraída pela possibilidade de economia de energia mecânica. Embora gaste mais energia que a moenda para lavar a cana, o difusor consome muito menos energia mecânica, porque utiliza apenas um terno para a secagem final do bagaço. Em média, segundo os especialistas, um difusor consome cerca de 35% da energia demanda por uma moenda - o excedente de vapor vivo pode ser usado para a produção de uma quantidade extra de energia nos geradores elétricos. A Noroeste planeja produzir 80 MW/h, dos quais 55 MW/h serão vendidos para concessionárias a partir do segundo semestre do próximo ano. "O cenário mundial indica racionamento a partir de 2009. A energia será produto comercialmente interessante para as usinas", acredita Miranda. A característica também foi um dos fatores que determinaram a escolha da Agro-Energética Monteverde pelo difusor. A usina está localizada em Ponta Porã/MS, com início de operação prevista para maio de 2009. Na primeira fase do projeto, a planta terá capacidade para processar até 1 milhão de toneladas de cana e produzir 20?MW de energia – o planejamento da empresa gerar 17?MW, dos quais 9?MW serão exportados. A usina atingirá seu limite de capacidade de processamento, 2 milhões de toneladas de cana, em 2012. Nesta etapa estará produzindo 50?MW e exportando 33?MW. "Além disso, estudos e testes sobre o uso da palha da cana como combustível da caldeira junto com o bagaço já estarão consolidados, o que abrirá mais uma possibilidade de ampliação do potencial de geração de energia", conta Würch. Embora a possibilidade de economia de energia mecânica represente vantagem em várias usinas, Fonseca alerta que o estudo de viabilidade deve considerar uma avaliação detalhada porque, dependendo do mix e da solução de fábrica da empresa, o ganho energético não se traduz em economia. No difusor o brix é baixo em relação à moenda, ou seja, tem mais água. "Para fabricar açúcar, tem que evaporar essa água, e há um gasto de energia. Se a usina for produzir açúcar e optar pelo difusor, a usina precisa avaliar o conjunto completo da planta", pondera. Mesmo nessas condições, um estudo mostrou a viabilidade do difusor na unidade São Francisco do USJ, que a partir de 2008 iniciará a produção de 80.000 MW de energia, volume já 100% contratado pelo o mercado – a unidade produz açúcar VHP para exportação. Segundo Ieda, o balanço de energia considera o brix menor e ainda se torna interessante na unidade. "Mas é preciso fazer um estudo completo e detalhado de uma unidade e fazer todas as adequações necessárias sempre de acordo com a tecnologia empregada", recomenda.
|
Tratamento de caldo contra pré-conceito
Com previsão de início de operações em abril de 2009 em cidade homônima no interior de Minas Gerais, a Usina Araguari terá capacidade para moer na primeira fase do projeto 1,5 milhão de toneladas de cana por safra, quantidade suficiente para a produção 750 milhões de litros de etanol. A Usina Araguari prevê produção açúcar na segunda etapa do projeto, quando vai moer 3,2 milhões de toneladas de cana por safra. O investimento total é superior a R$ 300 milhões, mas nenhum centavo será aplicado na aquisição de um difusor. A unidade até fez análise sobre o uso do difusor, mas a futura produção de açúcar influenciou a escolha por uma moenda (modelo MCD/01- 42"x 78"). "O sistema de extração por moenda facilita obtenção de caldo mais rico com melhor qualidade para a fabricação de açúcar. Um difusor precisaria de processo mais afinado e custoso para produzir qualidade", explica o diretor da Usina Araguari, Fernando Mello. A pior qualidade do açúcar produzido a partir de caldo extraído pelo difusor é um conceito disseminado no setor sucroalcooleiro que, segundo os fornecedores, ainda impede o maior crescimento do número de aplicações. "Este é um pré-conceito que ainda precisamos combater com maior intensidade", reconhece Marcos Fonseca. Os críticos avaliam que o açúcar adicional extraído pelo difusor em comparação com a moenda não é aproveitado porque a maior produção de melaço provoca perdas no setor de cozimento. A Uni-systems defende que o difusor permite a separação entre caldo primário (mais rico) e caldo secundário (mais pobre), que são retirados respectivamente do primeiro e do segundo captadores de caldo. "Além disso, o colchão de bagaço por onde o caldo percorre funciona como um filtro, diminuindo desta maneira a quantidade de impurezas levadas para o processo", argumenta Fonseca. Segundo o gerente de projetos da empresa, o segredo para a obtenção de açúcar de qualidade, produzido a partir de extração de difusor ou moenda, é o estabelecimento de um eficiente sistema de clarificação de caldo, capaz de remover grande parte dos componentes de cor. O procedimento é atestado pela unidade São Francisco do Grupo São João, projetada para a produção de açúcar VHP de alta qualidade – além de álcool anidro e hidratado. A usina planeja exportar 100% das 60.000 toneladas de açúcar VHP previstas para a safra atual, ampliar a produção para 350.000 a partir de 2009. A produção de VHP normalmente é destinada para China e Rússia, além de países do Oriente Médio, mercados considerados muito exigente. "Se for bem tratado, o caldo do difusor é de boa qualidade", garante o gerente industrial José Ieda Neto. O tratamento do caldo da São Francisco consiste na adição de cal no difusor para pH 7,2, aquecimento e introdução de polímero/descolorante. Posteriormente, o processo de decantação é realizado em decantador sem bandeja e peneiramento do caldo decantado. Segundo Marcos Fonseca, outro caso de aplicação de difusor para fabricação de açúcar é a unidade Cruz Alta da Açúcar Guarani, que também exporta o produto para diversos países. "À medida que difusor for sendo implantado em mais unidades, esse pré-conceito tende a acabar".
|
Divulgação/Uni-systems

|
|
Difusor da Açúcar Guarani/Cruz Alta – usina exporta açúcar para diversos países |
|
Redução de custos operacionais
O estudo de viabilidade da São Francisco também considerou outra característica, a possibilidade de redução de custos operacionais. Assim como a economia de manutenção, essa vantagem do difusor foi apontada por todas as usinas consultadas pela reportagem de Alcoolbrás. Segundo os entrevistados, uma instalação com difusor opera de forma automática e dispensa grande quantidade de profissionais durante a operação. Um painel central de controle permite que o processo seja controlado por um só operador por turno. "Além disso, cada terno de moenda exige um soldador em tempo integral. Se forem seis ternos de moenda, serão seis pessoas a menos por turno", comenta Würch. A unidade São Francisco ainda não atingiu a capacidade plena de processamento do seu difusor, de 12 mil toneladas por dia, mas já adianta que os resultados são positivos. "Uma de nossas premissas para este novo projeto era a redução drástica dos custos operacionais. Não temos cálculos exatos, mas posso adiantar que estamos atingindo esse objetivo", afirma Ieda. Diante das vantagens apresentadas pelas usinas que pioneiramente apostaram no difusor, os fornecedores acreditam que a participação do equipamento no mercado deve continuar crescendo gradativamente. Mas a tecnologia ainda vai precisar vencer alguns conceitos disseminados no mercado - como a dificuldade de produzir açúcar de qualidade e a flexibilidade de ampliação de moagem – para ameaçar o reinado das moendas. A discussão sobre qual é o melhor sistema é antiga e não há consenso no mercado – algumas características favorecem a moenda e outros resultados são melhores com o difusor. Os especialistas recomendam que a escolha priorize uma minuciosa análise que avalie quais vantagens de cada tecnologia oferecerão melhor retorno de investimento para as características de planta em questão. "Embora seja menos tradicional, vale a pena buscar informações sobre o difusor e consultar quem já opera o equipamento no Brasil", sugere Fonseca.
|
LEIA A MATÉRIA NA ÍNTEGRA NA EDIÇÃO
IMPRESSA |
Desejando saber mais sobre a matéria: redacao@editoravalete.com.br |
|
|
Matéria de Capa
Há vagas. Tratar: indústrias de Sertãozinho
|
|
Crystalsev e Dow elevam alcoolquímica a patamar industrial
|
Novo presidente da Abimaq quer combate a produtos chineses
|
Com abrangência nacional, Ceise quer se transformar em referência sucroalcooleira
|
|
|
|